The Basics Of The Pharmaceutical Manufacturing Process
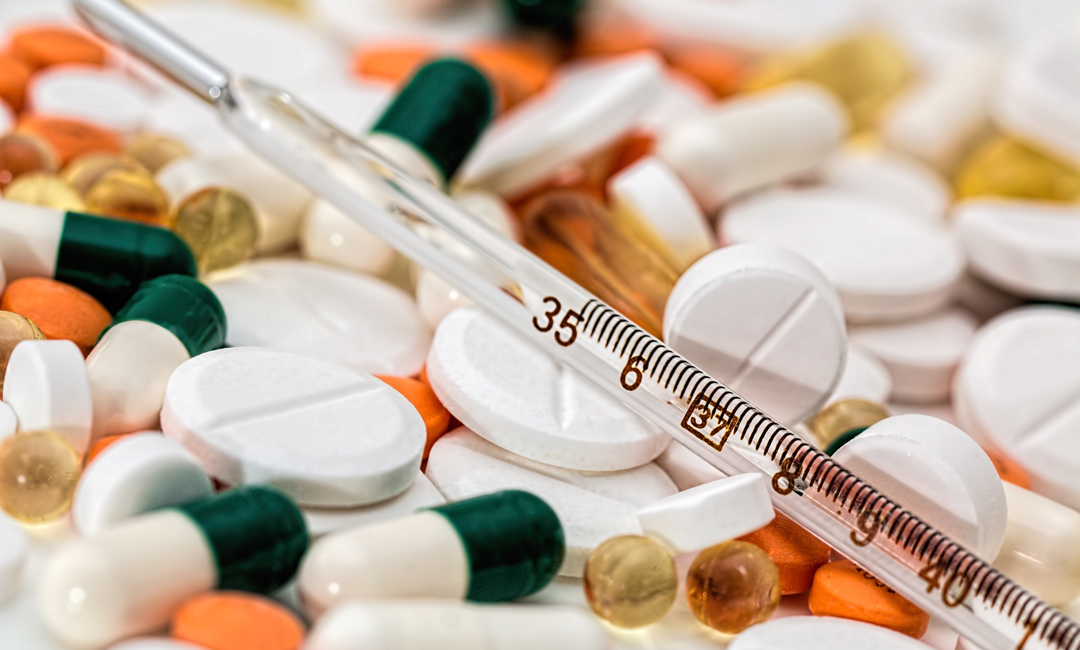
Health care systems worldwide rely on the pharmaceutical industry to supply them with the medicines they need to keep patients healthy or at least symptoms-free for as long as possible. The pharmaceutical industry includes both public and private organizations that operate in various areas of activity such as research and development, manufacturing, and marketing. Scientific research and development are the leading sectors of the pharmaceutical industry.
Breakthrough discoveries and technological advances are a solid foundation for the creation of new molecules and of effective drugs that provide enhanced healing effects and fewer side effects. Specialists from a wide array of sectors work together toward the creation and dissemination of drugs featuring higher potency and specificity.
The industrial-scale creation of pharmaceutical drugs is known as drug manufacturing. Pharmaceutics drug manufacturing processes consist of a series of steps such as milling, granulation, tablet pressing, and coating.
Main Steps Of The Pharmaceutical Manufacturing Process
A continuous manufacturing process requires the constant feeding of raw materials into the system, doubled by continuous extraction of finished products. The stability of the feeding rate is one of the key elements of a successful and efficient manufacturing process. Powder-based continuous processes call for accurate and consistent powder materials feeding into the production line. In order to achieve such high consistency and accuracy rates, pharmaceutical companies rely on top-notch feeders that are designed with such features in mind in the first place.
Oftentimes, the pharmaceutical manufacturing process requires the blending in of various non-active ingredients to create the final product used for the solid tablet. There are several factors that influence this process such as the particle form (spheres, cubes rods, etc.), the particle size variation, the powder flow properties, and the moisture levels among many others.
In some situations, the raw powders require milling, in order to bring the particle size to a more manageable value. The homogeneity and the dosage uniformity are only two of the benefits of milling. Furthermore, milling helps increase the solubility of the active compound. Many manufacturers use repeated powder blending followed by milling to achieve the desired manufacturability level.
In a way, you can consider granulation as being the opposite of milling. There are two basic types of granulation: dry granulation and wet granulation. Granulation helps prevent the “demixing” of the different compounds in a mixture, by creating granules that contain all of the ingredients in the right amounts. In addition, granulation improves compaction properties for the formation of solid tablets.
When it comes to manufacturing drugs with poor solubility and bioavailability, pharmaceutical companies use hot-melt extrusion. Occurring at the molecular level, this process helps disperse poorly soluble compounds in a polymer carrier. This process requires mixing the materials with the help of heat, pressure, and agitation.
The last step of hot-melt extrusion involves the actual extrusion of the raw material through a tool die. A twin-screw high shear extruder breaks up the particles and blends the materials, the resulting product being easier to compress into tablets or to fill into capsules.
Should the production process require reaction selectivity, companies may use ice to cool drugs. It’s worth mentioning here that the cooling process is quite complex when occurring at the industrial size. The process of cooling a standard reactor is expensive.
Furthermore, lowering the temperature may result in an increase in the viscosity of the reagent, making mixing more difficult. Flux pumps offer the world’s best drum and IBC pumps and complete system solutions to a comprehensive range of accessories, optimal performance, and operational safety with minimal downtime costs. The harder stirring and the more frequent repairs and parts replacement can contribute to increasing the production costs even further.